Cutting Molybdenum Wire
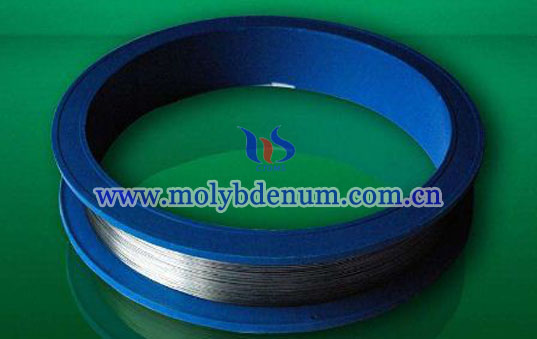
Cutting is a significant operation sequence to make finished molybdenum wire. While cutting, molybdenum wire may be broken. In order to process good products, processing technique must be paid great attention, and preventing wire breaking is one of it. There are three points to be noticed during cutting molybdenum wire:
Wire break when start to cut, molybdenum wire feed forward and touch workpiece, then it break. When molybdenum wire is outside of workpiece, the distance between up and down guide pulley is pretty big, molybdenum wire vibrates because there is no damping exist. It makes the gap between wire and workpiece is under bad situation, or there are too much cooling liquid, these factors reduce insulation resistance, under such kind situation, arc discharging will appear during electric discharging, arc discharging will burn molybdenum. For wire cut EDM machining, arc discharging is one of main reasons causes wire broken. And the bigger electric current is used, the more burned harm will happen to the wire, and it is much more probable for wire to break.
During cutting process. When wire cut deep in to workpiece, gap between wire and workpiece is too small to allow cooling liquid to get into workpiece. The carbon black and metal chip are not easy to be flushed out of workpiece. Such situation is getting working condition worse and worse. Just cutting thin workpiece, the gap is not stable and arc discharging is easy to happen, if arc discharging concentrate at a special area, it may burn molybdenum wire to break.
Wire break when cutting is about to finish. When there is still tiny distance left to cut. Except reason discussed above, weight of workpiece is also a very important reason for such kind wire broken, workpiece may deform due to stress, and workpiece break wire. Solution is to make special fixture and workpiece have to be heat treated.